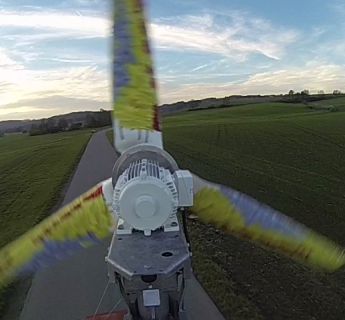
Bionic technology in its smartest application
learning from the role model of nature in applying next generation technology in wind energy.
AF-AX currently develops a surface technology for wind turbine rotor blades which is able to adapt the airfoil of the blade dynamically to the surrounding airflow by acting passively to the surrounding flow. By that it mimics the natural role model of a birds feather coating which by nature is equipped with the same feature to ensure high aerodynamic performance. Giving a rotor blade passive-dynamic reshaping abilities has the following benefits:
-
Rotor blades will increase lift and reduce drag by that the power output
of the turbine is significantly higher -
Stall resistant features ensure a fast spin up to react on any wind gust
-
By its dynamic reshaping ability it has a highly turbulent robust
feature ensuring permanent performance under almost any condition. -
Low wind sensitivity increases uptime and thus substantially more
power gain over time.